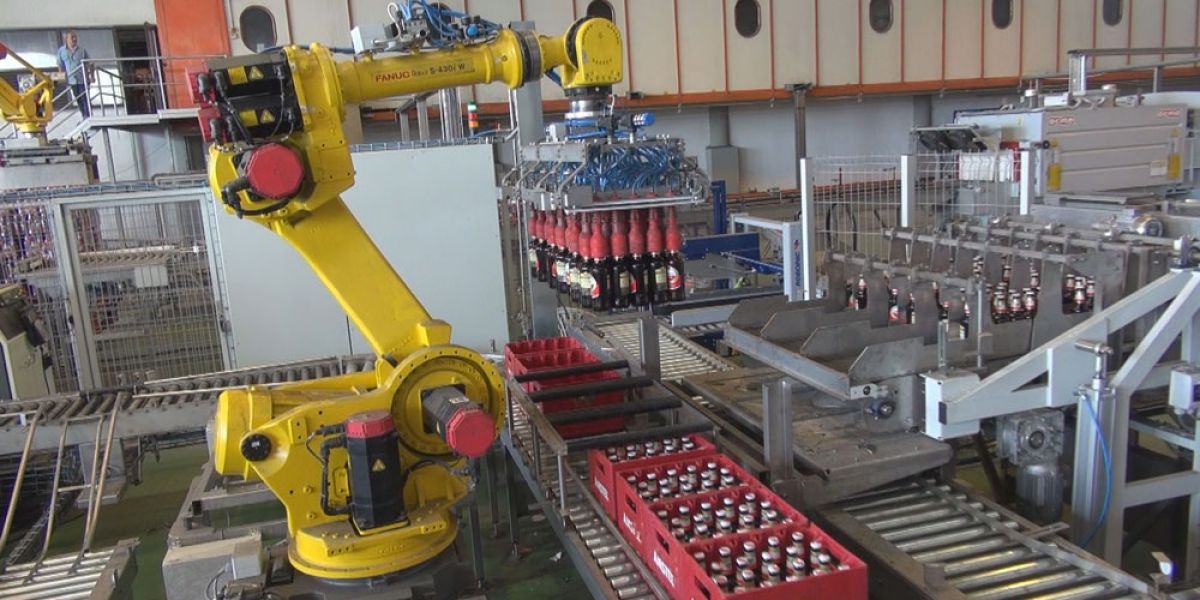
ARCON GROUP, компания с богат опит и експертиза в проектирането и внедряването на роботизирани и автоматизирани решения за края на производствената линия, успешно завърши инсталацията на напълно автоматизирана линия за пренареждане на стъклени бутилки за HEINEKEN.
Нуждата
HEINEKEN търсеше напълно автоматизирана линия за пренареждане на стъклени бутилки от пластмасови кошници в свити пакети за мултиопаковки.
Изпълнението включваше депалетизиране на пластмасови кошници, разопаковане на пластмасови кошници и подаване на стъклените бутилки към машина за мултиопаковки. Мултиопаковките трябваше да бъдат свити в пакети, кодирани и палетизирани. Освен това палетите трябваше да бъдат обвити в термофолио и групирани преди да бъдат изнесени от системата. Друга необходимост беше създаването на смесени пакети с шест броя, съдържащи два различни продукта (4+2). Линията трябваше също да има вторична функция – опаковане на бутилки в картонени кутии, вместо създаване на пакети с мултиопаковки.
Решението трябваше да отговаря на нуждите за висока производителност и оптимално използване на пространство и съществуващи ресурси.
Решението
ARCON проектира и предложи интегрирано и напълно автоматизирано решение, което напълно отговаря на нуждите на HEINEKEN. Линията за пренареждане, която беше изградена, имаше следните характеристики:
- Депалетизиране на пълни кошници
- Палетизиране на празни кошници
- Разопаковане на пълни кошници
- Първично опаковане на бутилки в свити мултиопаковки
- Кодиране на мултиопаковки (срок на годност, партиден номер) с Domino Inkjet принтери
- Вторично опаковане на мултиопаковки в свити пакети
- Етикетиране на пакети (срок на годност, описание, баркод) с принтери Print & Apply
- Палетизиране на пакети
- Обвиване на пакети с термофолио
- Система за наблюдение и управление
За вторичната функция на линията:
- Създаване на картонени кутии
- Опаковане на разопаковани бутилки в кутии
- Запечатване на картонени кутии
Три роботизирани клетки бяха проектирани и изградени за нуждите на горната система: една за депалетизиране на пълни кошници и палетизиране на празни кошници, една за разопаковане на бутилки и опаковане на бутилки в кутии и една за палетизиране на свитите пакети. Струва си да се отбележи, че три съществуващи роботизирани ръце, които бяха модифицирани и нагласени към нуждите на проекта, бяха включени в системата, което значително намали разходите по проекта.
Цялата опаковъчна линия също така включва: два термофолийни машини, машина за създаване на кутии, машина за запечатване на кутии, индустриален принтер с термично мастило, система за етикетиране с Print & Apply, машина за обвиване с термофолио и пълна система за обработка на продукти.
Освен проектирането, изграждането и интеграцията на решението, АРКОН разработи SCADA система, която позволява синхронизация и безпроблемна работа на цялата система. Тази ИТ система позволява графично представяне, наблюдение и управление на линията и нейната производителност в реално време, като предоставя полезни данни за производството. Проектирането на решението гарантира лесна употреба, адаптивност към бъдещи нужди и висока производителност.
Контролни панели на системата са оборудвани с тъчскрийн екрани с различни възможности като показване на грешки и графично представяне на производителността на системата и дистанционна техническа поддръжка. Системата разполага с множество предварително инсталирани производствени програми, които покриват нуждите на различни продукти, така че промяната на продуктите става автоматично и мигновено, без нужда от промени в настройки, освен избора на продукт.
Важно е да се отбележи, че е била разработена многозонова система за безопасност, която осигурява съответствие както с CE нормите, така и със строги изисквания на клиента, без да се компрометира производителността на линията.
Ползите
- Увеличена производителност (до 21 000 бутилки/мин)
- Намаляване на производствените разходи
- Надеждност и минимални нужди от поддръжка
- Гъвкавост и разширяемост, тъй като системата лесно може да бъде надграждана и модифицирана за нови продукти
- Оптимално използване на ресурсите (пространство, работна сила, съществуващо оборудване и ИТ системи)
- Минимални оперативни изисквания
- Минимизиране на грешки
- Бърза и точна следпродажбена поддръжка
Ако сте заинтересовани от подобно решение, моля, попълнете формата за контакт по-долу или ни пишете на
Храни и Напитки